Introduction:
Copper, an extraordinary metal known for its excellent electrical conductivity and thermal properties, holds immense potential in the world of CNC precision machining. As a manufacturer of CNC precision instrument accessories, it is crucial to explore the advantages and opportunities presented by copper machining. In this article, we will delve into the remarkable attributes of copper and highlight the numerous benefits and exciting possibilities it offers in the realm of machining.
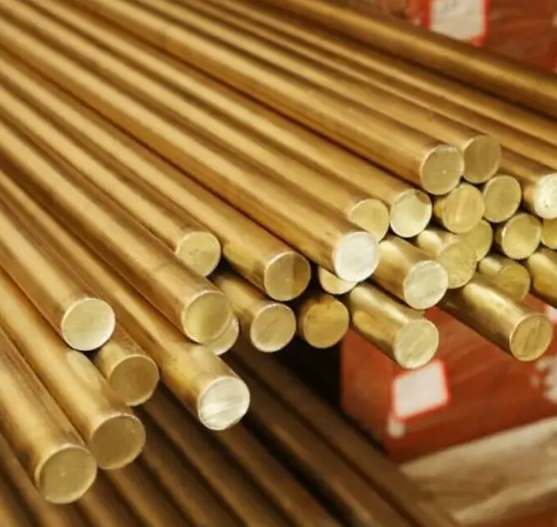
1. Exceptional Electrical Conductivity:
Copper stands out as a superior choice for precision instrument accessories due to its unparalleled electrical conductivity. Its low electrical resistance allows for efficient and reliable transmission of electrical signals, making it ideal for applications involving connectors, contacts, and conductive components. By harnessing copper's conductivity, manufacturers can ensure optimal performance and accuracy in precision instruments, enabling seamless data transfer and functionality.
2. High Thermal Conductivity:
In addition to its exceptional electrical conductivity, copper boasts remarkable thermal conductivity. This property makes it invaluable for precision instrument accessories that require efficient heat dissipation. Heat sinks, cooling plates, and other thermal management components benefit greatly from copper's ability to rapidly transfer heat away from critical areas, ensuring the reliability and longevity of sensitive instruments. By utilizing copper in machining processes, manufacturers can enhance the thermal performance of precision instruments, preventing overheating and maintaining optimal operating conditions.
3. Machinability and Precision:
Copper offers excellent machinability, making it a preferred material for
CNC Machining. Its softness and ductility enable easy cutting, milling, and shaping, resulting in precise and intricate designs. Copper's malleability also reduces tool wear, ensuring prolonged tool life and increased productivity. The ability to achieve tight tolerances and intricate details with copper machining allows manufacturers to produce high-quality precision instrument accessories that meet the stringent demands of various industries.
4. Corrosion Resistance and Durability:
Copper possesses remarkable corrosion resistance, making it an ideal choice for precision instrument accessories that may encounter harsh environments or corrosive substances. Its natural oxide layer acts as a protective barrier, preserving the integrity and functionality of components over extended periods. Whether used in medical equipment, aerospace applications, or electronic connectors, copper's corrosion resistance ensures durability and reliability, even in challenging conditions.
5. Versatility and Integration:
Copper's versatility and compatibility with other materials make it an invaluable resource in CNC machining. It can be seamlessly integrated with materials like aluminum, steel, or plastics to create hybrid components that leverage the unique advantages of each material. Furthermore, copper can undergo various surface finishes and coatings, allowing for customization and optimization according to specific application requirements. This flexibility enables manufacturers to meet diverse industry needs while maintaining the exceptional attributes of copper.
6. Expanding Applications:
The applications of copper machining continue to expand across industries. In electronics, copper is extensively used in the production of PCBs (Printed Circuit Boards), connectors, and wiring harnesses. The medical field benefits from copper's biocompatibility, employing it in surgical instruments, imaging equipment, and electronic implants. Aerospace and automotive industries leverage copper's lightweight nature and electrical conductivity in components such as sensors, connectors, and electrical systems. Furthermore, research and development laboratories rely on copper machining to create precision instrument accessories and high-frequency RF (Radio Frequency) components.
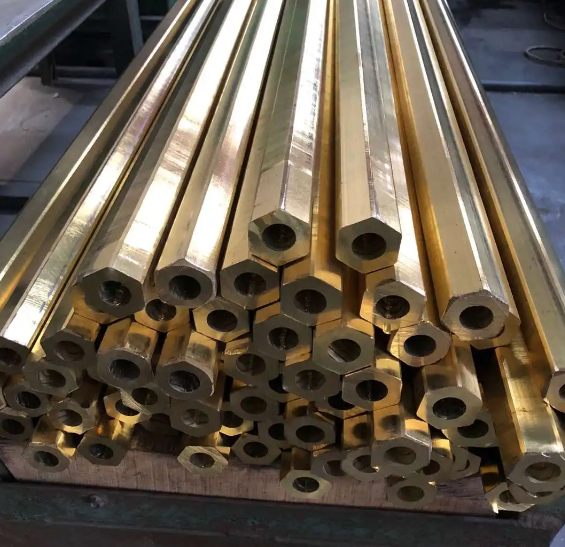
Conclusion:
By harnessing the power of copper through precision machining, manufacturers of CNC precision instrument accessories can unlock a multitude of advantages and opportunities. From its exceptional electrical conductivity and thermal properties to its machinability, corrosion resistance, and versatility, copper emerges as a valuable material for the production of high-performance precision instruments. As we continue to explore and innovate in copper machining, we can expect to see exciting advancements and endless possibilities in precision engineering and beyond.