Introduction:
In the realm of precision instrument manufacturing, the advent of Computer Numerical Control (CNC) has revolutionized the industry, transforming the way components are designed and manufactured. CNC technology has become a cornerstone in the production of CNC precision instrument accessories, bridging the gap between design concepts and tangible reality. In this article, we will explore the power of CNC in machining and manufacturing processes, highlighting its benefits and the impact it has on the precision instrument industry.
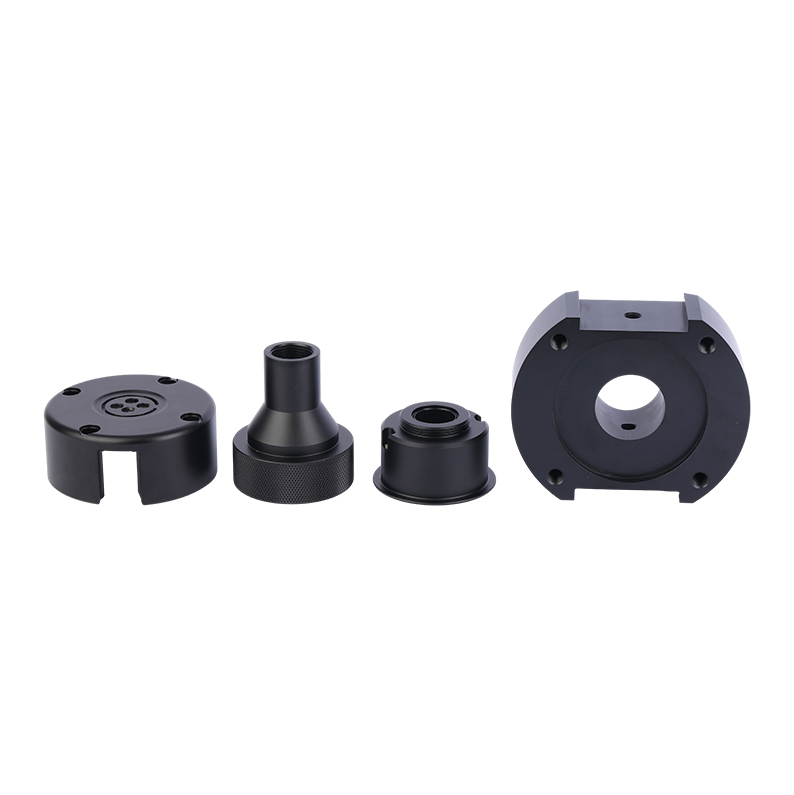
1. Precision and Accuracy:
CNC Machining brings unrivaled precision and accuracy to the manufacturing process. Utilizing computer-controlled systems, CNC machines precisely follow programmed instructions to execute complex machining operations. This precision ensures consistent quality, tight tolerances, and impeccable dimensional accuracy in the production of precision instrument accessories. Manufacturers can rely on CNC technology to deliver components that meet the most stringent specifications, enhancing performance and functionality.
2. Flexibility and Versatility:
CNC machines offer exceptional flexibility and versatility in machining and manufacturing processes. They can be programmed to create a wide range of precision instrument accessories, adapting to diverse designs, shapes, and materials. CNC technology allows for the efficient production of complex components with intricate details, ensuring consistent quality across different production runs. Manufacturers can leverage the versatility of CNC machines to respond to market demands, customizing designs and swiftly adapting to changing requirements.
3. Enhanced Efficiency and Productivity:
CNC technology significantly enhances efficiency and productivity in machining and manufacturing processes. With automated operations, CNC machines streamline production, reducing human error and minimizing production time. Once a program is set, CNC machines can work tirelessly, 24/7, optimizing production output and meeting tight deadlines. This increased efficiency translates into higher productivity, shorter lead times, and improved overall manufacturing capacity, allowing manufacturers to meet customer demands effectively.
4. Complex Geometries and Intricate Designs:
CNC machining enables the production of precision instrument accessories with complex geometries and intricate designs that were once challenging or impossible to achieve manually. By utilizing advanced CAD/CAM software, designers can create detailed digital models, which are then translated into machine-readable code. CNC machines precisely execute these instructions, resulting in components with intricate features, contours, and fine details. This capability expands design possibilities and facilitates the creation of innovative precision instrument accessories.
5. Consistency and Reproducibility:
CNC technology ensures consistency and reproducibility in precision instrument manufacturing. Once a program is developed, CNC machines can replicate it accurately, producing identical components with high precision and consistency. This capability eliminates variations that may occur in manual processes, ensuring that each produced part meets the same specifications and quality standards. Consistency and reproducibility are critical in precision instrument manufacturing, guaranteeing that every component performs reliably and consistently.
6. Material Optimization and Waste Reduction:
CNC machining allows for material optimization and waste reduction. Through efficient toolpath planning and nesting techniques, CNC machines can minimize material waste, maximizing the utilization of raw materials. Additionally, CNC machines enable precise cutting, reducing the need for secondary operations and minimizing material loss. This waste reduction not only contributes to cost savings but also aligns with sustainable manufacturing practices, reducing environmental impact.
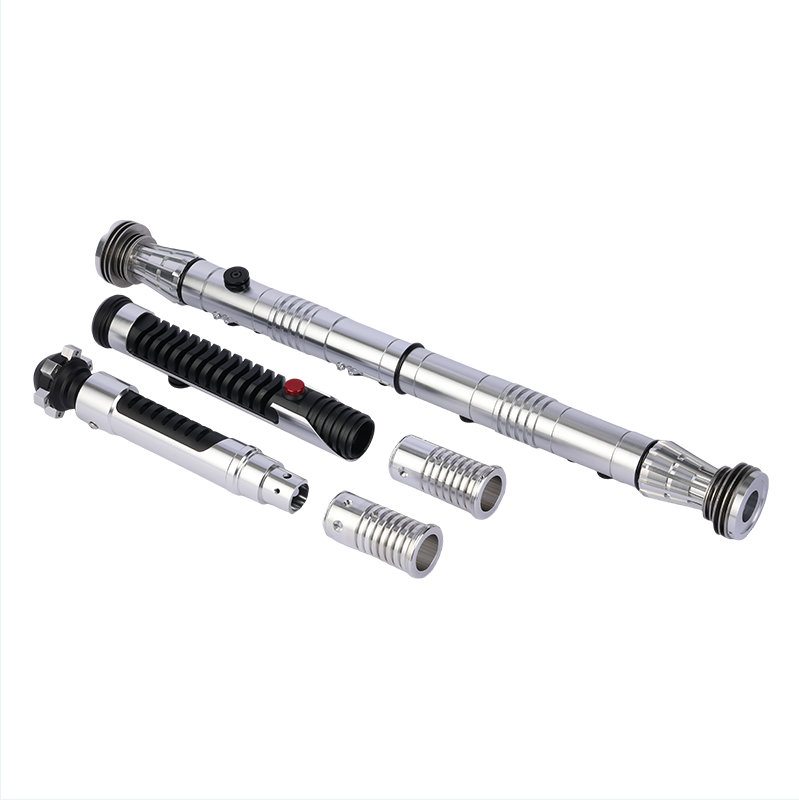
Conclusion:
The power of CNC in machining and manufacturing processes has transformed the precision instrument industry, offering unprecedented precision, flexibility, and efficiency. CNC technology brings designs to life, ensuring accuracy, consistency, and reproducibility in the production of precision instrument accessories. By harnessing the capabilities of CNC machines, manufacturers can deliver components with intricate designs, tight tolerances, and exceptional performance. The integration of CNC technology in precision instrument manufacturing paves the way for innovative advancements, shorter production cycles, and increased customer satisfaction. From design to reality, CNC technology continues to shape the future of the precision instrument industry.